I. Overview
A high-power wheeled tractor independently developed by China Yituo Group Co., Ltd., the rear transmission case is not only large in size but also very complicated in structure (see Figure 1). The outer dimensions are 1050mm × 925mm × 750mm, and the
Casting volume is about 0.085m3. The theoretical weight is about 615kg.

In this trial production, this shell part adopts the lost foam casting technology, and this technology is used to produce thin-walled shell parts with such large volume and weight and complicated structure, which are rarely reported in existing journals and magazines. Through repeated trial production, it is found that the castings after casting have the following three problems: First, the deformation of the castings makes the dimensional accuracy of the castings difficult to guarantee; secondly, the inner cavity of the castings is easy to form iron-clad sand, which increases the difficulty of cleaning; third is the surface of the castings. There is a defect in the formation of carbon black, which causes the scrap to be scrapped during the processing of the casting.
There are many factors that cause the above-mentioned casting defects, but the coating plays a vital role in the entire lost foam casting process. If the coating itself is improperly formulated, the coating performance is poor, which not only can not effectively solve the problem, but will cause defects.
(1) Poor paintability of the coating The paint for production test is water-based paint, and the white mold of the rear transmission case is made of polystyrene foam, which is not easily wetted and infiltrated by water-based paint. The wettability is not good, the coating is poor, the coating can not be hanged on the surface of the white mold or the adhesion is not good. On the one hand, the pattern will be coated many times, and in the process of multiple coating and drying, the tendency of the white mold to be deformed is increased. On the other hand, the coating thickness is uneven, even the coating is discontinuous, and the white mold is partially exposed to cause sticking sand defects. Due to the large size of the white mold of the rear transmission case (see Figure 2), the buoyancy generated during dip coating will cause the pattern to break. Therefore, the application of the white mold is a combination of spraying and showering. The coating properties of the coating put forward higher requirements.
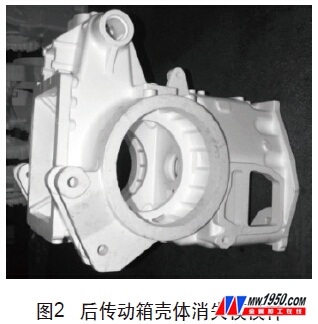
(2) After the strength of the paint is low, the white mold of the transmission case has a large volume, a thin wall and a small density, and the entire white mold does not have an inherent rigidity. The coating at room temperature has low adhesion strength, which is easy to cause peeling and damage of the coating during drying and handling. It is impossible to ensure that the pattern has sufficient resistance to deformation during the sand filling and compaction process, resulting in deformation; the high temperature strength of the coating is not High, in the high temperature state, it is impossible to prevent the damage of the coating during the casting of the molten metal and during the forming process, resulting in defects such as collapse of the box, sand sticking, etc., thereby failing to ensure the dimensional accuracy and surface quality of the casting; the residual strength of the coating is poor, which may result in It is not easy to clean the coating from the surface of the casting after casting.
(3) Poor gas permeability of the coating material Because the material of the prototype is HT250, the casting temperature is controlled at 1380 to 1430 °C in the production test, and the material of the white mold is polystyrene foam. The material is in the temperature range of 1350 to 1550 °C. It begins to crack rapidly, burns vaporization, and the low molecular weight polymer cracks rapidly, depositing a large amount of hydrogen and free carbon. If the permeability of the coating is poor, a large amount of pyrolysis products cannot be smoothly exported through the coating, which will cause pores in the casting; if the coating cannot absorb the residue generated when the polystyrene foam is burned, the casting is prone to residual carbon inclusion defects. .
In view of the casting defects caused by the coating in the technical background, the development of the coating formulation is emphasized, and the mixing process of the coating is also explored.
Second, the development of coating formulations
1. Composition and material selection
(1) Refractory powder lost foam coating has three important requirements for the selection of refractory powder: First, the particle size of refractory powder should be coarse, but too coarse, the anti-sand property of the coating will be affected, taking into account the anti-stick sand And high gas permeability, the choice of particle size is 0.08 ~ 0.071mm (180 / 200 mesh); Second, the more rounded the refractory powder, the better the roundness of the powder, the third is the refractory powder The foam-like cleavage product has an adsorption capacity. In order to improve the overall performance of the coating, high alumina bauxite clinker powder (particle size 0.08 mm) and mica powder (particle size 0.071 mm) were selected for the refractory powder. The high alumina bauxite powder is porous and has a round shape, which can improve the gas permeability of the coating and the adsorption capacity of the foam cracking product; the mica powder is structurally a layered structure silicate, which has heat resistance and wear resistance. Insulation performance, good elasticity and flexibility, adding a certain proportion of mica powder to the coating can improve coating coverage, high temperature permeability and sinterability.
(2) Binder lost foam coating adhesive is an important part of the coating, which not only imparts strength and coating properties, but also affects the breathability and suspension of the coating. In general, the combination of an inorganic binder and an organic binder not only ensures the normal temperature and high temperature strength of the coating, but also effectively improves the gas permeability of the coating. Due to the large volume and thin wall of the transmission case and the transmission case, in order to ensure the rigidity, strength and permeability of the coating, white latex, alpha starch and RSF powder with wetting adhesive are selected. The mixture is mixed in a certain ratio. In particular, the selection of RSF powder effectively improves the stiffness, strength and coating permeability of the coating.
(3) The main function of the carrier liquid is to disperse the refractory powder. In the lost foam casting, water is used as the carrier liquid in consideration of various requirements such as environmental protection, application, drying, gas generation and cost. The coating is obtained in good suspension, paintability and non-flowing properties.
(4) Suspension of suspension paint directly affects the coating ability and coating quality of the coating, and also affects the handling performance of the coating. Because the particle size of the refractory powder is coarse, the viscosity of the coating is large. When formulating the coating, Lithium bentonite and attapulgite are used as suspending agents. Lithium bentonite and attapulgite can form a three-dimensional network structure in water, and the combination of the two has a significant effect on improving the suspension property of the coating and improving the rheology and process performance of the coating.
(5) There are three main types of auxiliary additives.
1 defoamer. It is used to eliminate bubbles formed by the paint during the production process.
2 surfactants. A small amount of surfactant is added to the coating, the main purpose is to improve the adhesion of the coating to the pattern and facilitate application.
3 preservatives. In order to facilitate the storage and long-term use of the paint, a certain amount of preservative is added to the paint, which can effectively prevent the mold from undergoing mildew and deterioration in the high temperature season and losing the viscosity.
2. Formulation of lost foam casting coating formulation Through repeated trials, the amount of each component in the coating was continuously adjusted, and the formulation of the coating was finally developed (see Table 1). According to this formulation, the formulated coating was subjected to a production casting test.
Third, coating performance research
1. Test method for coating properties
(1) Measurement of paint density The density of the paint was measured by a 100 mL graduated weighing method.
(2) Test of suspension stability of paint A method of measuring the deposition rate of 6 h using a 100 mL measuring cylinder was used.
(3) The concentration of the paint is tested using a Baume meter (for production sites).
(4) Test of coating thickness The prepared foam sample 100mm × 100mm × 12mm (preferably taken from the scrapped white mold), immersed in the mixed paint for 10s, taken out and put into the electricity at 50 °C In the drying oven, after 3 hours of drying, the test piece was taken out and the thickness of the coating was measured.
(5) The high-temperature gas permeability and high-temperature strength test of the coating adopt the multi-functional performance tester developed by Huazhong University of Science and Technology. 2. Properties of the lost foam coating According to the above coating formulation, the performance of the test coating was tested. The results are shown in Table 2.
Fourth, the preparation process of the coating
Many experiments have found that the performance of the coating is not only related to the coating formulation, but also related to the preparation process of the coating. The same formulation and different preparation processes have great influence on the performance of the coating. In order to obtain a coating with good process performance, the preparation process should ensure that the thixotropic agent, binder and solvent are sufficiently dispersed, and strongly adsorbed with the refractory powder, so that the components of the coating are fully fused, so that the coating has good thixotropy and Spreading.
1. Coating preparation equipment
High-speed dispersing mixer, roller-type sand mixer.
2. Preparation method
(1) Preparation of wet powder coating The weighed refractory powder is poured into a roller-type sand mixer. After mixing for 5 to 10 minutes, the binder, suspending agent and auxiliary additives are poured into the mixture. In the mill, after mixing for 30 to 40 minutes, the milled bag is ready for use.
(2) Preparation of slurry coating Weighing a certain amount of wet powder coating, according to the ratio of powder to water ratio of 1:0.6-0.7, weigh the quantitative water into the paint mixing tank, and place the paint bucket under the high-speed dispersing mixer. Open the high-speed dispersing mixer, then add the weighed wet powder coating, stir at high speed (800 ~ 900r / min) for about 40min, then stir at low speed (<600r / min) for 2h, stir the uniform paint, and let it stand for 24h. It is fully matured, and the moisture can be adjusted according to the requirements of Baume.
V. Casting test
According to the coating formulation of Table 1, according to the coating preparation process, the prepared slurry coating material is poured into the self-developed application device, and the white mold is applied, dried, shaped, and poured. The test condition is shown in Fig. 3 and Fig. 4 ,Figure 5.
Conclusion
(1) Adding an appropriate amount of mica powder to the refractory powder, the coating's coating and suspension properties are improved, and when the sample is applied, a thicker coating can be obtained at one time, which reduces the number of coatings and simplifies the pattern. The production process; adding the appropriate amount of mica powder, in the case of the same coating thickness, the overall weight after the coating is applied, the stiffness and strength of the pattern can be effectively ensured; adding the appropriate amount of mica powder reduces the bauxite powder coating Sintering temperature, after casting, the coating is easy to peel off from the casting, and the surface of the casting is smooth.
(2) In the coating formulation, the wetting agent RSF powder is added, the adhesion of the coating to the foam pattern is obviously enhanced, and the strength of the coating is improved, which is important for ensuring the rigidity and strength of the pattern.
(3) Lithium bentonite and attapulgite are used together, according to the mixing process formulated for the lost foam coating, it is verified that the process properties such as suspension, thixotropy and coating of the coating are significantly improved, and when applied to the pattern, the coating is applied. The layer thickness is uniform, which avoids the problem of sticking sand caused by the white mold being exposed.
About the author: Chen Li, Bao Zheng, Institute of Process Materials, First Tractor Co., Ltd.