1 Introduction There are many kinds of automobile parts, and generally have the characteristics of complex shape, variable structure and high density. The parts are produced using almost all
Casting processes including high pressure
Die Casting, low pressure casting, gravity casting,
Sand Casting. The generation and improvement of casting casting defects have a great relationship with the choice of casting process. Casting of automotive castings is difficult and generally has the property of producing large quantities. Therefore, how to accurately analyze the location and cause of various defects, quickly obtain methods to eliminate defects, shorten the trial production cycle and reduce the cost of parts production are key issues that enterprises need to solve.
Since the flow and solidification process of the metal melt in the cavity cannot be visually seen in the actual production process, it often takes a lot of time and trial production to solve the casting defect problem and it is difficult to achieve the best effect. The application of casting simulation analysis technology can help technicians to intuitively analyze the flow and solidification process of the melt inside the cavity. Before the actual test, the casting may have defects, its size and position. Effectively shorten the trial production cycle, reduce production costs, and improve the core competitiveness of enterprises. At present, domestic casting simulation analysis technology is beginning to be popularized and applied, and casting simulation software has been basically popularized in foundry enterprises in developed countries. Especially in the US and European automotive mold manufacturing enterprises, casting simulation analysis has become an indispensable means. More and more domestic companies have begun to pay attention to the huge economic benefits brought by casting simulation software.
2 high pressure die casting engine block example At present, the manufacturing process of engine cylinders is mainly gravity casting and high pressure die casting. High pressure die casting has the characteristics of high production efficiency and good working environment. Many enterprises have adopted high pressure die casting to produce engine cylinders. However, high-pressure die-casting requires a relatively high level of mold design. If the mold design is not good, it will directly affect the product's pass rate.
According to the design scheme and process plan of a high-pressure die-casting engine block mold manufacturer, the simulation analysis is carried out. The three-dimensional shape of the product is shown in Figure 1. The process design die casting temperature is 680 ° C, the mold preheating temperature is 180 ° C, the room temperature is 25 ° C, the die-cast aluminum alloy is ADCl2, and the die steel is SKD61. The barrel diameter is 134 mm, the speed in the low speed zone is 0.25 m/s, the speed in the high speed zone is 2 m/s, and the low speed transition time is about 0.147 s.
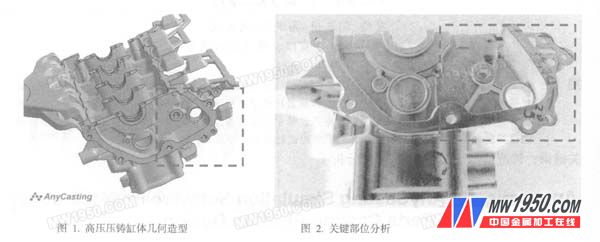
When designing the high-pressure die-casting cylinder mold, firstly pay attention to setting the flow channel and slag package to ensure that there are no pore defects in the cylinder. In this paper, the improvement of the pore defect in a certain position is taken as an example to introduce the AnyCasting software in the improvement of the gas defect. Application.
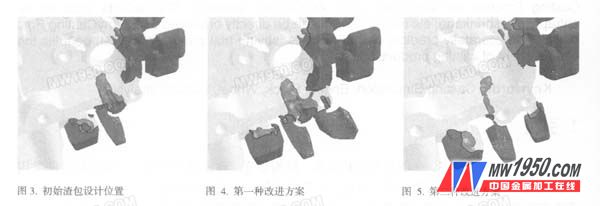
As shown in Figures 3 to 5, by predicting the position of the gas, the position of the slag bag can be accurately designed to reduce the volume of gas or even the gas, and to avoid the influence of the pore defects on the quality of the casting.
3 low pressure casting car wheel examples The main production process of automobile wheels is low pressure casting. The development of the pressure curve in the low-pressure casting process and the shrinkage and shrinkage between the spokes and the rim are frequently encountered in the production of automobile wheels. This paper introduces a series of pressure adjustment process setting process for liquid lifting, filling and holding time of a low pressure casting wheel hub, and effectively reduces or even eliminates shrinkage and shrinkage to produce high quality castings by placing a cooling device on the mold. Successful instance.

The low pressure hub pressure regulation process diagram in this paper is shown in Figure 6. Figure 7 shows the phenomenon of splashing during filling. This filling pressure curve design is unreasonable. The filling process has a great influence on the porosity defects. The pressure relief began after 303 seconds of pressure retention, and as a result, the nozzle portion of the riser tube was blocked by the solidified aluminum alloy, as shown in FIG. After adjustment, an appropriate dwell time is obtained. The adjusted process is shown in Figure 9, which ensures the solidification of the casting and ensures that the riser is not blocked.
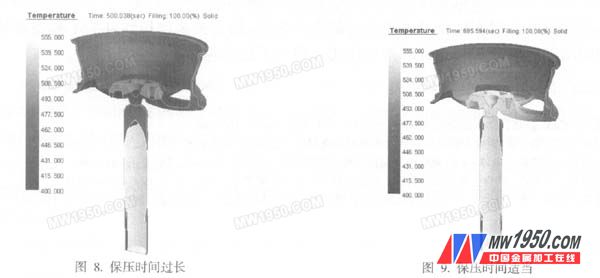
Low-pressure automotive wheel castings often exhibit shrinkage and shrinkage defects at specific locations. The usual practice of eliminating shrinkage defects is to add a cooling system to the mold. Therefore, the setting of the cooling system, the setting position and its effect on the casting are problems that engineers pay more attention to. It is the most common to install water pipes and air-cooled pipes at the upper and lower molds. Since the machining of the side molds is more complicated than the water-cooling and air-cooling pipes of the upper and lower molds, the cooling pipes are not added to the side molds.
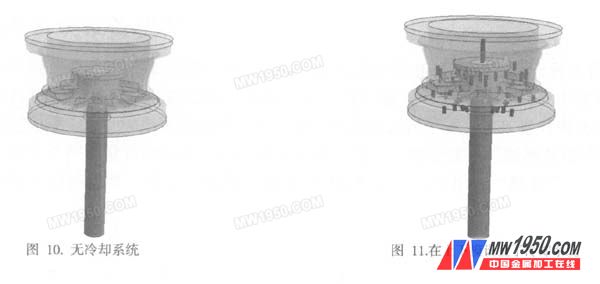
In the example in this paper, the prediction of the shrinkage and shrinkage position of the castings in the case of no cooling system and cooling system is compared. Figure 10 and Figure l1 show the upper and lower molds and the riser tube before and after the cooling system. In the three-dimensional shape, the distribution of water-cooled and air-cooled tubes can be observed in Figure 11. By comparison, it can be clearly seen that the mold of the cooling system is provided, and the molded wheel hub member is obviously improved in the shrinkage and shrinkage at the intersection of the spoke and the rim, and other positions are also improved.
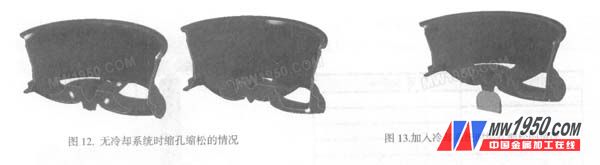
4 Conclusion (1) The Anycasting casting simulation software was applied to simulate the high-pressure die-casting engine block. The simulated gas-filled position was found in the actual castings, and fine pores were found. Through reasonable addition of slag package, the simulation was obtained. Good results; after the mold has been modified, the quality of the actual castings has also been improved.
(2) Simulation analysis was carried out using the pre-designed casting process of low-pressure automobile hubs. The problems in filling and holding process were found, which effectively guided the process improvement of the process design department. Through the analysis of the shrinkage and shrinkage of the hub castings, the position of the cooling system and the effect of the system are determined.
(3) Introduce the case of the combination of the simulation analysis of the high-pressure die-casting engine cylinder and the low-pressure casting wheel hub and the actual production. It can be seen that the casting simulation software has a guiding role for the actual production process. With the continuous improvement of casting simulation software and the increasing experience of enterprise use, its guiding role in process design has also been recognized by more and more enterprises.